More news
- Focus on the global coatings market: Global coatings market outlook
- View from the UK: Navigating chemical policy and sustainability
- Focus on adhesives: Unveiling unbreakable bonds – Testing redefines physical strengt...
- Focus on adhesives: Henkel and Covestro collaborate for sustainability of engineered wood ...
- Advances in construction chemical technology: What’s new in 2024?

Global warming is causing increasingly erratic weather all around the world. Severe heat can contribute to massive service interruptions, especially when temperatures soar. Here, Maria Lamorey, Commercial Strategy Manager for PPG industrial coatings, discusses how the proper coatings to help preserve power generators, transformers, switchgear and more have never been more crucial
The years-long tight supply chain for critical electric distribution equipment like transformers shows no signs of easing. That’s not good news for utility companies trying to keep up with demand just as storm season is upon us. Since the onset of the global COVID-19 pandemic in 2020, raw material shortages, shipping issues, labour challenges and increasing electricity demand have created a perfect storm. These challenges are creating shortages that are impacting the availability of equipment and parts essential for power distribution with wait times up to four times longer than pre-pandemic times.
The challenges are even greater considering the renewed calls for energy independence and the growing use of carbon-free sun- and wind-based sources. This rise in renewable energy requires an expansion of the energy grid to accommodate new equipment and transformers at a time when the supply chain is stretched beyond capacity.
Low inventory of parts, coupled with an ageing energy infrastructure, are putting vital systems like hospitals, communications, waste and water and even military bases at risk. According to the U.S. Department of Commerce, the average age of transformers in the field is 38 years, nearly the end of the expected service life, with 70% older than 25 years. With new equipment in short supply, maintaining and refurbishing existing equipment is paramount. Restored and repaired transformers can be installed in the field within just a few months, which can help meet rising demand.
A key part of this refurbishing process is updating the exterior protection, including sanding, priming and painting with a durable industrial coating engineered to defend against corrosion. While it’s never an ideal time to change coatings systems, this slowdown represents an opportunity for manufacturers to evaluate their current protective technologies to determine if newer ones are available that may offer more robust and resilient protection.
Considering their exposure to extreme weather conditions, outdated and substandard coatings systems can lead to impairments and disruptions in power services. Unfortunately, equipment breakdowns and repairs are especially problematic in this current climate.
READ MORE:
PPG marks strong progress against 2030 sustainability targets with latest report
Strong defense against corrosion
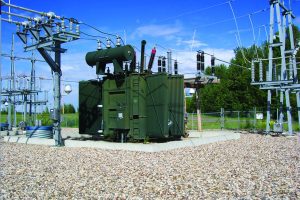
When it comes to the metal components on a transformer, corrosion is public enemy number one and prevention is the top line of defense. Metal electrical equipment parts corrode for any number of reasons. Some factors include the intersection of two metals with different corrosion thresholds, or continuous or repeated exposure to high temperatures and humidity from decades in the field, damaging pH (acid) levels, electrolytes, chemicals and ultraviolet rays from sunlight.
Coatings are the first line of defense to safeguard this critical infrastructure in the face of a variety of conditions. Selecting the proper coating materials to help preserve power generators, transformers, switchgear and more is crucial. The right coating system that offers durability and resilience at every layer of protection—from pretreatment through finish coat—can extend the service life of the part and reduce the risk of coatings-related failures of substation components.
While most electrical equipment has a minimum life expectancy of 20 years, many components are expected to survive 50 years ormore. Harsh elements can accelerate corrosion and leave sensitive instrumentation vulnerable during storms and compromise its reliability. Unfortunately, many manufacturers still combine old “cut-and-paste” specifications that date back 20 to 30 years with current industry-standard regulatory requirements written by IEEE, UL, CSA and ASTM when painting and protecting new equipment. On average, finished electrical components are composed of about 70% metal and 30% non-metal substrates, yet nearly 100% of electrical equipment manufacturers view painting metal as beyond their core competency. An average-sized switchgear manufacturer running 10 to 15 million square feet of coated metal through its facility is staking a lot of its reputation on work considered outside of their scope. If the goal of an electrical equipment manufacturer is to build next-generation components that exceed performance mandates while protecting its brand reputation, paint specifications should be reviewed and updated regularly. In addition to product scope and substrate type, manufacturers should address the following criteria:
Coating type
Coating manufacturers offer a variety of resin chemistries to improve resistance to corrosion and UV exposure, including epoxies, polyesters, urethanes and acrylics, as well as hybrid coatings, which incorporate a combination of resin chemistries. Each have their strengths and weaknesses. For instance, epoxies are ideal for chemical resistance and mechanical properties, but are lacking in UV resistance and weatherability. Polyesters, urethanes and acrylics all offer exceptional weathering characteristics, but each offers a different benefit, such as great physical properties for polyesters; chip, scuff and mar resistance for urethanes; and exceptional surface appearance for acrylics.
Product codes
Electrical equipment producers should avoid using a specific paint manufacturer’s product code. Codes can be ambiguous or difficult to find, as they often change or may be unique to a specific customer. Instead, detail the specific coatings technology the equipment demands (pretreatment, liquid, powder or electrocoat); then detail the resin chemistry of the desired coating.
Colour
Establishing and maintaining a standard colour can be challenging. It is important to detail an acceptable range of colour variation and use a proven and consistent method for determining that the colour of a painted parts falls within specification. Pantone, RAL, Munsell, and ANSI are colour-cataloging systems commonly used for these purposes, although some equipment manufacturers choose to create their own in-house standards. Maintaining colour standards is a whole separate topic, so it is best to work with a reputable paint manufacturer to understand the intricacies of creating a colour standard and how to detail its parameters in the specification.
Gloss
Like the colour spec, the gloss range specification can have a big impact on a product’s finished appearance. It is important to provide a specific gloss range in a paint specification, as variations in gloss can cause the same colour on a piece of equipment to appear as different shades.
Texture
In the electrical industry, some orange peel (minor paint dimpling) in the finish is considered preferable, as it tends to hide flaws andwear well over time. Regardless, standards for texture types and variation should be written into the paint specification.
Product handling and storage
Manufacturers suggest specific rules for handling and storage in their product data sheets, including an acceptable range of temperature exposures and fixed expiration dates to ensure inventory is properly rotated.
Performance
Regulatory standards such as UL or IEEE should be detailed in the paint specification. These standards are written to include a range of acceptable results for products undergoing laboratory-based performance tests, which have been agreed upon by the industry for their ability to mimic real-world performance environments.
Performance testing for expected service life
While many coatings systems are robust enough to pass industry-accepted performance tests, they can sometimes fail in the fieldbecause the real-world conditions are often more challenging. For that reason, it is critical to write into the paint specification the tests that most accurately reflect a product’s ability to fulfill a warranty or an expected service life. For example, does a specific impact test predict paint chipping once installed in the field? Or does an accelerated weathering test depict the real-world color fade or breakdown of a coating?
Performance testing must also correspond to field troubleshooting. If a coating fails in the field, correlating the failure to a specific testing method will enable the equipment and paint manufacturers to identify the reason for the failure more quickly, which can also lead to quicker solutions for corrective actions. Some of the most common performance tests written into an electrical equipment paint specification include: Salt spray; ultraviolet accelerated weather testing (QUV); simulated corrosive atmospheric breakdown (SCAB); humidity testing; impact resistance; cross hatch adhesion and gravelometre. Other tests that are occasionally used and built into specifications for electrical equipment include: Pencil hardness and adhesion testing. There also are many types of chemical tests, including an insulating fluids test to determine a coating system’s ability to resist exposure to certain types of chemicals.
READ MORE:
Reintroducing the wheel: Linseed paint as the natural option
Consider the coating
Is your current coating technology utilising the latest coatings advancements while also factoring in sustainability? Liquid coatings use solvents or water and are applied to pretreated metal with electrostatic spray, dipping and other conventional methods before being air-dried or force-cured. When used as part of an integrated primer, pretreatment and topcoat system, liquid coatings offer exceptional resistance to corrosion and chemicals, excellent sag resistance and strong adhesion. The newer product offerings in waterborne liquid technologies can offera sustainable option as part of an integrated coating layer.
Powder coatings are formulated for applications that require the ultimate combination of corrosion resistance, weathering performance and operational attributes. These coatings are typically formulated with specific resins combined to provide excellent corrosion and chemical resistance, as well as all-around application versatility. Since powder coatings are made without solvents, they generate virtually no volatile organic compound (VOC) emissions, which can help to achieve environmental compliance and reduce material usage, energy consumption and maintenance costs thanks to a first- pass transfer rate of up to 85%.
PPG scientists recently developed a Coil Primer Powder Topcoat (CPPT) system that replaces the standard Direct-to-Metal (DTM) powder process with the addition of a durable liquid primer basecoat. Instead of steel coils being sent directly to the fabricator or manufacturer, they are first shipped to a coatings applicator where the coils are unrolled, cleaned on both sides, coated with a primer and cured. The sheets are recoiled and packaged for shipment, ready forfabrication and powder coating process.
Cleaning the substrate is critical in the powder coating process. This system transfers this important yet laborious pretreatment functionto the applicator, saving the manufacturer time and money by eliminating the need for cleaning chemicals, hazardous wastewaterremoval and the labor needed in the process. The result is a more streamlined production process that increases throughput, makes compliance with environmental regulations easier to achieve, and adds an extra layer of protection with a factory-applied, baked on primer that can extend the lifecycle of the parts.
Summary and suggestions
When creating a paint specification, it is critical to correlate a device’s expected service environment and service life to the testing methodology that most rigorously replicates the performance challenges it will face. Not only will this help to ensure that a product performs reliably throughout its lifetime; it may also lessen maintenance requirements for that device duringits service life as well.
Equipment manufacturers should evaluate their paint specifications on a regular schedule to ensure that they always incorporate the most targeted and technologically advanced coating systems and testing methodologies for a specific application. They may also want to consider partnering with paint and pretreatment suppliers in the design process as early as possible, preferably with a proven coatings company that can offer both pretreatment and paint capabilities as an integrated package.
Integrated, full-service coatings suppliers typically have a deep understanding of the coatings process from start to finish, along with a wide range of products and resin chemistries that have been tested according to industry- standard criteria. These coatings suppliers can act as a partner in identifying potential vulnerabilities to corrosion and help customers to select the right products to prevent it. Most integrated coatings suppliers also have dedicated lab resources, which enables them to recommend the best test methodologies to measure a product’s potential service life and troubleshoot general coatings-related production problems.
The article is by Maria Lamorey, a commercial strategy manager at PPG. With more than 20 years of industry experience, Maria plays a leading role in PPG’s commitment to delivering high-performance coatings products across a variety of general industrial applications including electrical equipment of all types. View the white paper here.